At Bauma, the upgraded 850 G hybrid materials handler will likely be one in every of 10 machines on show at Sennebogen’s sales space within the outside space (FM.712).
With a attain between 17m and 21m, the 850 G hybrid can be utilized in a variety of purposes, together with for demanding metal scrap dealing with and port dealing with. Its modular design allow the machine to be configured in line with buyer necessities, together with with undercarriage variants from stationary to cellular.
As a part of a rightsizing, the brand new materials handler now has a 231kW Stage V diesel engine which runs at a normal velocity of 1725rpm. This not solely reduces gas consumption, but in addition the machine’s noise emissions in the long run. As well as, particular eco settings and the choice of fuelling the machine with HVO allow sustainable operation. Furthermore, large-dimensioned hydraulic valves and contours allow optimum effectivity ranges and supply aid for the pump system.
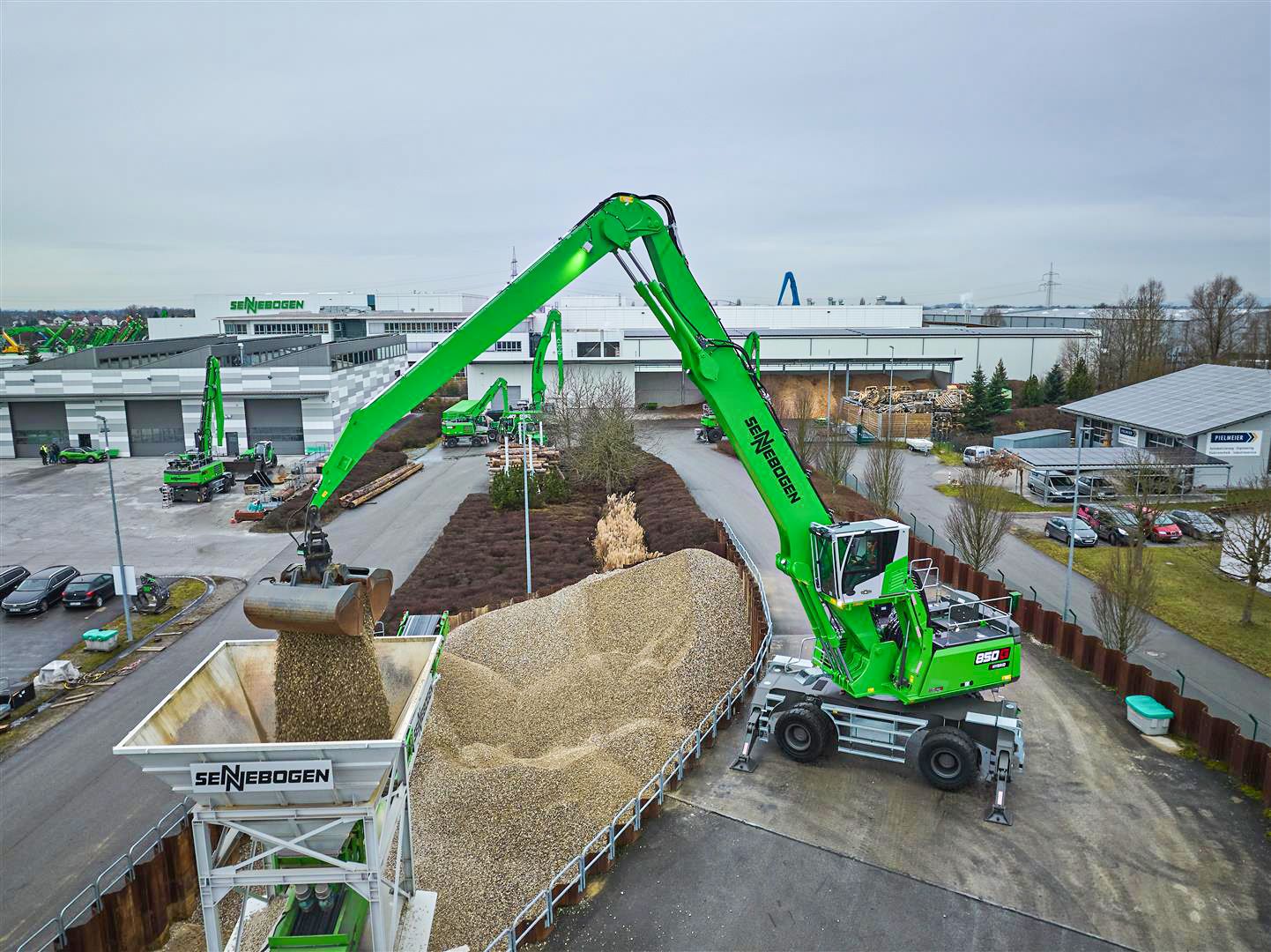
The main advantages in vitality saving and effectivity come from the Inexperienced Hybrid recuperation system which has been built-in for the primary time in a machine of this measurement. The vitality restoration system consists of a gasoline stress accumulator put in within the rear of the machine and a 3rd hydraulic cylinder on the increase. Much like a tensioned spring, this technique shops the vitality generated when the increase is lowered within the nitrogen accumulator and releases it again into the lifting cylinders throughout the subsequent lifting operation. This protects round 30% gas which equates to round 22 tons of CO2 per yr. On the similar time, the machine’s output is elevated by 80kW to a complete system output of 311kW.
The usual cab elevation has been considerably stabilized by the centrally articulated cab raise cylinder and elevated to 2.80m so {that a} snug viewing top of 6.10m is achieved with an non-obligatory top of 6.80m. The Maxcab includes a utterly revised inside design with a give attention to ergonomics and luxury. The brand new automated air con system features a whole of 10 built-in air vents to make sure an optimally tempered working setting regardless of the climate.
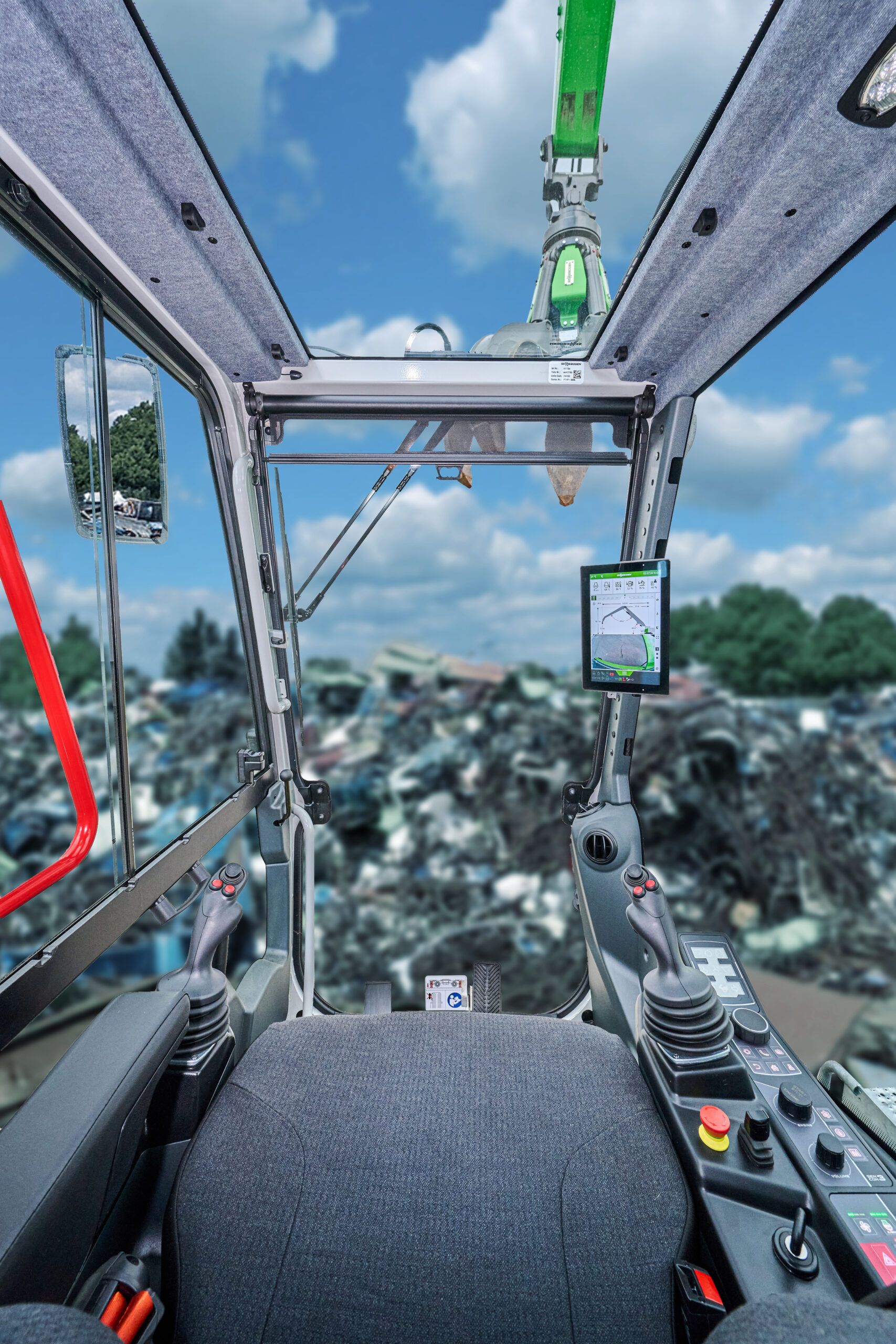
The center of the brand new Maxcab is the 10-inch contact show which gives fast entry to all necessary capabilities which might be assigned to buttons and switches with customization choices. The driving force can be supported by clever help techniques that not solely put together the machine for (partially) automated operation sooner or later, but in addition guarantee optimised efficiency and elevated security when dealing with the machine now.
The brand new Sencon management system will increase the communication functionality of the fabric handler, which isn’t solely useful for the operator, but in addition for the machine proprietor or fleet operator. The reference to the Sennebogen telematics system Sentrack supplies a considerable amount of knowledge which permits the operator to derive analyses – for instance on efficiency or machine situation.
As well as, concrete price financial savings might be made by avoiding on-site customer support visits. Networking with the Sennebogen troubleshooter helps the operator to rectify errors independently. Customer support can connect with the machine and provide options remotely and software program updates will also be put in remotely.