The battery enclosure is a central element of a battery-electric automobile. Welding its varied elements presents particular challenges for the welding know-how used. Scansonic now provides the ALO4 collection of laser welding optics, offering appropriate options for every of those duties. Mixed with accessible laser beam sources and a wire feeder, a complete system for laser beam welding on this essential utility space is now accessible.
Though the automotive trade is at present present process structural adjustments, it’s sure that the way forward for passenger automobiles will probably be battery-electric. The precise timeline for this transformation stays open, however all producers are already persistently aligning their mannequin ranges in the direction of electromobility. This shift has far-reaching implications for manufacturing: whereas conventional areas similar to engine and transmission manufacturing are shedding significance, new necessities are coming into focus. One of many central challenges is establishing appropriate manufacturing applied sciences for collection manufacturing. The manufacturing of the battery enclosure is especially within the highlight, contemplating the basic parameters of commercial mass manufacturing: cycle time, high quality, and price.
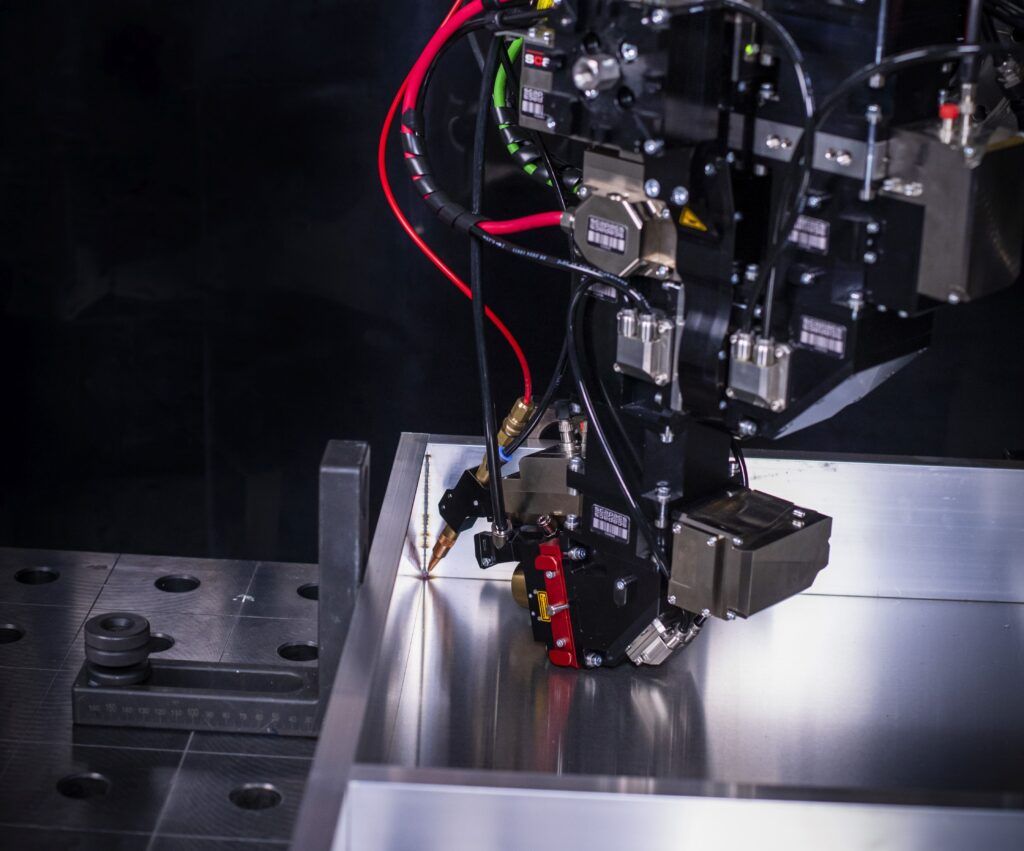
Complicated Battery Enclosures
The lithium-ion batteries utilized in electrical automobiles are mechanically delicate and have to be reliably protected towards impacts, excessive temperatures, and moisture. Accordingly, excessive calls for are positioned on the battery enclosure: it have to be sealed, have excessive rigidity, and embody constructions for cooling the cells. On the identical time, low weight and economical manufacturing prices are important. In most automobile ideas, the battery pack is built-in into the automobile ground, reducing the middle of gravity and growing passive safety within the occasion of an accident.
In collection manufacturing, most OEMs depend on battery enclosures manufactured from aluminum. The decrease weight in comparison with metal has a direct constructive influence on vary. Aluminum-magnesium-silicon alloys of the 6000 collection are sometimes used, as they provide a superb weight-to-strength ratio. Nevertheless, a specific problem arises from their elevated tendency to type sizzling cracks – a facet that locations particular calls for on the welding course of.
Along with the fabric, the geometry of the battery enclosure additionally locations excessive calls for: several types of weld seams similar to fillet welds, butt welds, and T-joints have to be reproducibly joined with top quality. Overlap joints can have gaps attributable to manufacturing tolerances that have to be reliably bridged throughout the welding course of.
Challenges of Laser Welding
For the weld seams required within the battery enclosure, laser welding provides decisive benefits over typical strategies. It permits excessive processing speeds with exact vitality enter – relying on the appliance, the welding velocity will be about twice as excessive as arc welding. The low warmth enter additionally considerably reduces the chance of deformation of the element throughout the becoming a member of course of.
Regardless of these benefits, many producers have to this point hesitated to make use of laser know-how persistently, as appropriate optics weren’t accessible for all becoming a member of factors. A mix of laser and arc welding inside the identical manufacturing facility typically appears impractical for mass manufacturing.
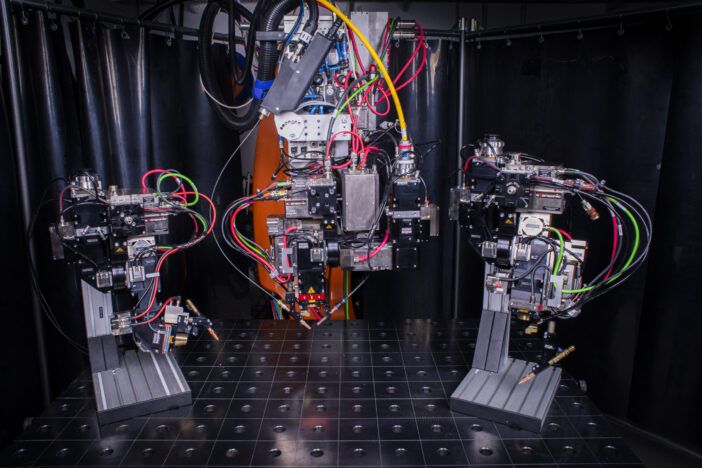
Appropriate Laser Welding Optics for All Necessities
Scansonic, a number one producer of laser processing optics for 25 years, has particularly developed its established ALO4 to satisfy the necessities within the battery enclosure sector. The ensuing household of processing optics now covers all welding duties on this space. A further wire is used within the course of. This not solely reinforces the seam but additionally ensures, with the so-called tactile seam monitoring, that the processing all the time takes place precisely on the fringe of the element.
Particularly for hot-crack-prone aluminum alloys of the 6000 collection, the extra wire provides an efficient strategy to course of stabilization, notably concerning the formation of sizzling cracks. Gaps as much as one-third of the thickness of the higher element will be reliably closed – the ensuing weld seams are steady and crack-free.
Even bigger tolerances will be bridged if the optic is moreover geared up with beam oscillation. In growing the ALO4-O, the engineers utilized current know-how for each tactile and distant welding processes. The ALO4-O combines tactile seam monitoring with the laser beam oscillation of a distant optic. Two synchronized scanner axes allow oscillations of the laser beam as much as 1,000 Hz. Oscillation form, amplitude, and frequency are freely programmable. The method will be designed in order that materials from the higher element is melted and used along with the extra wire for hole filling – tolerances as much as 50 p.c of the fabric thickness will be compensated. The beam oscillation additionally provides important benefits for processing thicker sheets, such because the battery enclosure lid, because it achieves a large seam reference to a smaller laser beam focus. This implies much less warmth enter in comparison with a bigger spot with out oscillation.
Changes for Geometrically Demanding Joints
Some weld seams have to be made contained in the battery enclosure – with correspondingly restricted accessibility for the software. The ALO4-L laser welding optic was developed for these purposes. Its prolonged telescopic arm permits deeper penetration into the battery enclosure; the working distance is about 70 mm better than the opposite variants of the ALO4 household.
For vertical seams inside, the collection was additionally expanded with the ALO4-F. This optic makes use of a 3rd deflection mirror that deflects the beam by 115°. This permits the vertical seams within the corners of the battery enclosure to be reliably reached and welded.
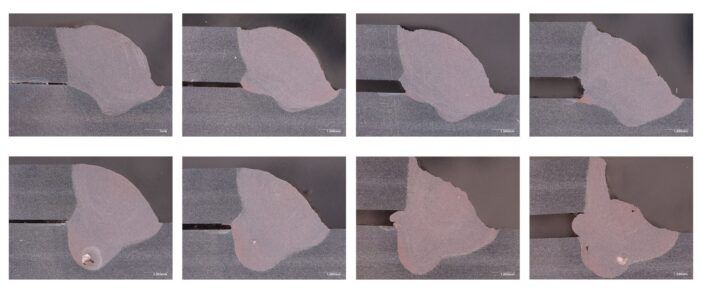
A Persistently Coordinated Full System
The coordinated use of the 4 ALO4 variants brings important benefits for manufacturing. The widespread management system mechanically acknowledges which ALO4 optic is linked and adjusts the parameters accordingly. Upkeep and spare elements stock are additionally simplified by systematic standardization.
The processing optics are appropriate with all widespread laser sources in the marketplace. For even simpler integration, Scansonic provides all different system elements together – together with the wire feeder from Dinse and appropriate laser sources from Brightlight Laser Methods – from a single supply. The result’s an optimally coordinated full system with excessive course of reliability.
All variants of the ALO4 collection can be found with the SCeye course of monitoring system developed by Scansonic. This absolutely paperwork the welding course of. AI-based algorithms detect pores and spatter that escape from the soften pool. Moreover, all related machine and course of parameters are constantly monitored – an necessary foundation for seamless high quality assurance in collection manufacturing.